 |
Automatic
adjustment to fuel type
What fuel will
you be using to operate your boiler? Today it may be spruce wood chips direct
from the forest, but tomorrow your local furniture factory may supply you
with very dry hardwood waste as fuel. This is no problem for an ETA boiler!
With the
help of the lambda probe, the regulator in the ETA HACK measures the flue gas
oxygen and adjusts the input of fuel as well as the air intake
for combustion depending on the energy density of the wood currently being
burnt.
Industry
standard
Rough industrial
standard wood chips from a sawmill can also be handled without any
difficulty. The feeder screw has a diameter that allows for pieces up to 5 cm
square (G50) to be conveyed smoothly into the boiler. The auger through is designed
so that there is space on top of the screw to carry extra long pieces with a
length of up to 12 cm and a cross-section up to 5 cm in diameter.
The pitch
of the conveyor screw increases progressively along the length of the
enclosed through, loosening and separating the chips as they progress. This
ensures that the flow of fuel is both smooth and quiet.
|

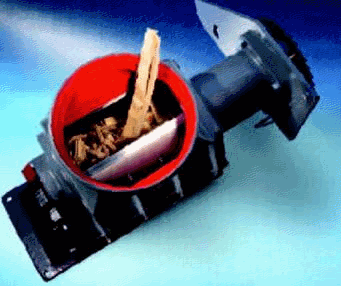
|
 |
WITH A
SINGLE CHAMBER ROTARY VALVE YOU ARE PROTECTED AGAINST BURN BACK.
An air tight,
single chamber, rotary valve installed in ETA’s wood chip boilers, sets new
standards of safety. In contrast to conventional fire protection flaps, this
single-chamber wheel design means that it can never be in a position which
allows a direct connection between the fuel store and the combustion area. No
furnace gas can enter the fuel feeder and prematurely ignite the wood chips.
This is the most reliable possible protection against burn-back.
The
single-chamber rotary valve has been newly developed by ETA to handle wood
chips up to G50 in size. Excessively long pieces of wood are cut as they
enter the chamber with a toughened, and replaceable, blade. Only a small
minimal amount of power is needed to drive both the stoker screw and the
one-chamber rotary valve, so you have maximum safety with low electricity
costs
|
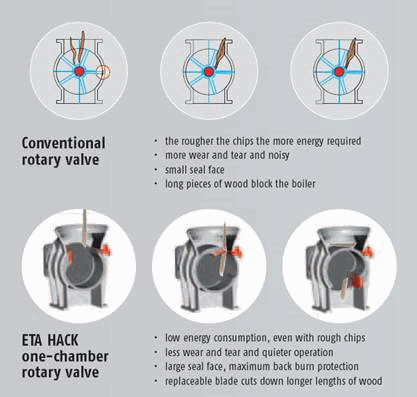 |
BETTER PERFORMANCE WITH LESS ELECTRICITY
The types of worm gearboxes which are often found in conveyor screws achieve
a level of efficiency of around 65%. The component gears used in ETA’s wood
chip feeder systems are top quality helical gears which work with 95%
efficiency. These gears, combined with the progressive screw, can lead to a
reduction in electricity consumption of more than 30%.
The new
220 volt single phase wood chip boiler released by ETA in late Autumn 2007
allows for greater flexibility in installation location and means that rotary
converters will no longer be required on sites where 3 phase power is not
available
|
NO
BLOCKAGES
The amount of electricity required by the motor is constantly monitored and
so any blockages or resistance that builds up in the feeder screw is
immediately registered. This triggers the screw to briefly run in reverse.
This backwards movement is repeated up to three times which releases any
pieces of wood or small stones jammed in the screw. The fuel feed can then
proceed unhindered. When the feeder screw is running in reverse, the agitator
on the bunker floor is automatically taken out of gear. With the agitator in
neutral, all the power from the motor is directed towards dealing with the
obstruction in the feeder screw.
|
AUTOMATIC
ASH-DISPOSAL SYSTEM
A boiler always works most efficiently when it is clean – and stays clean –
throughout the heating season. And so, any automatic wood- burning heating
system must provide for automatic ash removal throughout the system: from the
grate to the heat- exchanger.
Turbulators
keep the heat exchangers tubes clear through a daily cleaning process and the
fire grate is regularly tilted to empty ash and debris build up. Two conveyor
screws, driven by a single motor, carry the ash from the collection bin under
the grate and also the fly ash from the heat exchangers, to the main ash bin.
This can then simply be removed from the front of the boiler.
There are no narrow sections in the ash channels so it is not possible for
stones or nails to block them
|
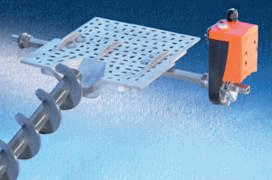 |
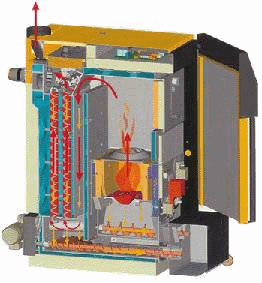 |
HOT
FURNACE WITH TILTING GRATE
Within a
refractory-lined furnace, the wood flame is mixed with the turbulent
secondary air. This guarantees that the fire burns cleanly with a high
combustion temperature even when fed wood chips containing up to 40% moisture
content
Without having to pass through any corners or narrow points the chips are
pushed on to the grate sideways. At pre-determined intervals, depending on
the heat output level at which the boiler is set, and when combustion is
complete, the grate is tilted to 90° in order to remove ash and any foreign
bodies from the burning areas. The tilting grate allows users to burn fuel
that contains stones, debris and even nails without any related problems
|
LIMITED
HEAT LOSS BETWEEN FIRINGS
The fire can be
regulated between minimum and maximum settings. To satisfy moderate heating
needs during autumn and spring, interrupting the burning process controls the
heat output. Because incomplete combustion would lead to a build-up of soot
in the boiler and flue, the fuel is therefore allowed to burn fully down
before the interval. After burning off, the primary and secondary air-flaps
are closed, and there is no air flow through the boiler and so no waste heat
passes up the chimney.
|
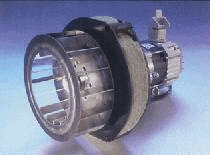 |
INDUCED
DRAFT
The
tried-and-tested induced draught technique (i.e. without a combustion air
fan) commonly used when burning wood logs and pellets are also applied by ETA
to burning wood chips. A quiet expulsion fan at the exit point of the boiler
keeps the pressure in the boiler low, thus ensuring high operational safety
and no risk of flash-back. The air-tight one-chamber rotary valve means that
a usual combustion air fan is not necessary. The air required is drawn in
through the regulated primary and secondary air flaps as a result of the
vacuum within the boiler.
Of course, a system with an induced draught fan and no ignition fan operates
with less electricity - the ETA HACK needs only 76 watts. And this already
low consumption is improved even further because of the speed regulator.
OPTIMUM
IGNITION CYCLE
After stopping the furnace for just a short while, the refractory-lined
chamber still remain hot enough for any new fuel which is fed in to be
spontaneously ignited by remaining embers. It is only necessary to start the
ignition fans if the fire has been out for a longer period of time.
However, feedback from the lambda sensor and the exhaust temperature ensure that the fans are switched off, in order to save electricity, as soon as the
fire has caught hold
FITS ALL CHIMNEY STRUCTURES
The wood chip
heating systems from ETA can be adapted to all types of chimneys. The induced
draught fan fits into small diameter
|
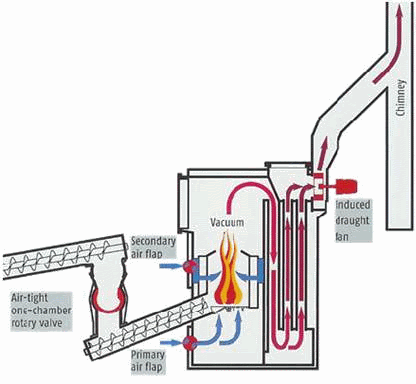 |
chimneys. The speed regulator controlling the draught and the continuously regulated flaps controlling the input of the combustion air mean that no
draught limiters are needed in the chimney. By setting the exhaust
temperature, condensation is avoided in the brick-lined chimney and, modern
stack design, this exploits the benefits of the low temperature
serviceability
CONVENIENCE
AND ECONOMY
The regulation of
an ETA heating system is convenient and cost efficient throughout – from the
function of the furnace, to the warmth supplied by the radiators or
under-floor heating in your home. Solar panels can also be integrated,
allowing the system to be regulated as a whole.
There’s no need to worry about with complex electronics. Once the settings
for the boiler have put in, information about its current status is given in
the four-line text display panel. If you want to change the heating time
settings, an easy-to-follow information text takes you through the procedure.
The various individual heating circuits can easily be adjusted. The desired room temperature can be set using a remote control, and the systems can also
be switched from day-time to night-time
|
ACTIVE
CONTROLS ENSURE RELIABLE OPERATION
The reliability
of operation of ETA systems is ensured by comprehensive measurement and
feedback of information about the status of all components and functions of
the system (speed of induced draft fan, position of air flaps, oxygen level
in the chimney flue, flue temperatures and water temperatures).
If a large stone or similar object blocks the fuel supply screw, instructions
on how to quickly deal with the problem are given on the display panel.
LAMBDA
CONTROL
If there is a
lack of air, complete combustion cannot take place. Whereas, if there is too
much air, the warmth produced by the boiler is not fully utilized, too much
of the warmth being produced simply passes up the chimney as wasted exhaust
gas and the efficiency is reduced.
The
lambda control regulates the primary and secondary air depending on the type
of fuel currently being burnt in order to achieve a high degree of efficiency.
INTELLIGENT
“BUS” CONNECTS BUILDINGS
If a number of
properties are connected to one central heating system or if the boiler is
located in a separate building – the ETA HACK is equipped with a “bus”
regulator to manage this.
The
heating circuits and hot water tanks in the external buildings are connected
via a CAN-bus to the boiler control. In this way, the readings from all parts
of the installation are constantly available so that the total heating needs
and consequently the regulation of the furnace can be controlled
|
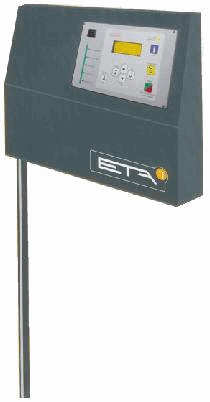 |
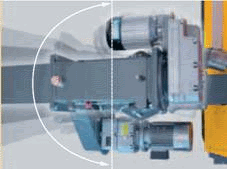

|
A
Perfect Fit with the ETA “Building Block” system
The well thought
out building block system keeps construction time down and makes it possible
to assemble a very flexible feed system from a number of standard components.
Boiler
will be supplied with a stoking mechanism on either the right or left hand side
of the boiler main body. On the side opposite the feed system there are no
parts requiring maintenance which means that the boiler can be placed up
against a wall to save space.
The
conveyor screw links distances of up to 8 meters. The connection between the
conveyor screws is a 1 3/8” splined shaft, commonly used on drive shafts in
agricultural machinery. Conveyor casings are connected by bolted flanges.
This makes installation simpler by avoiding the need to cut and weld. By
replacing or adding sections of conveyor screw (standard lengths in multiples
of 12.5cm) it is easy to adjust the overall length of the feeding screw.
Fuel
Feed
A floor
agitator is the most effective way to move fuel from the fuel bunker to the
boiler through the conveyor screw. Again ETA’s building block approach to
installation of your heating system means that various sizes of sprung blade
agitators are available – agitator diameters range from 1.5 to 6.0 meters.
|
A charge
screw conveyor with a diameter of 250mm and a transport capacity of 30 m3/h,
makes it possible to feed fuel into otherwise inaccessible cellar areas.
The ETA
range of fuel storage equipment also covers special needs and includes an
hydraulic scraper floor for large fuel bunkers, a rotating pivot auger screw
for high silos as well as link and inclined screw conveyors to overcome
differences in height
|
UNIVERSAL
JOINT:
By using
a globe joint at the connection point between the feeding screw and the
single chamber rotary valve. The gradient and angle can be varied up and down
and from left to right giving greater flexibility for boiler positioning
|
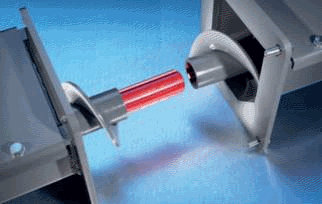 |